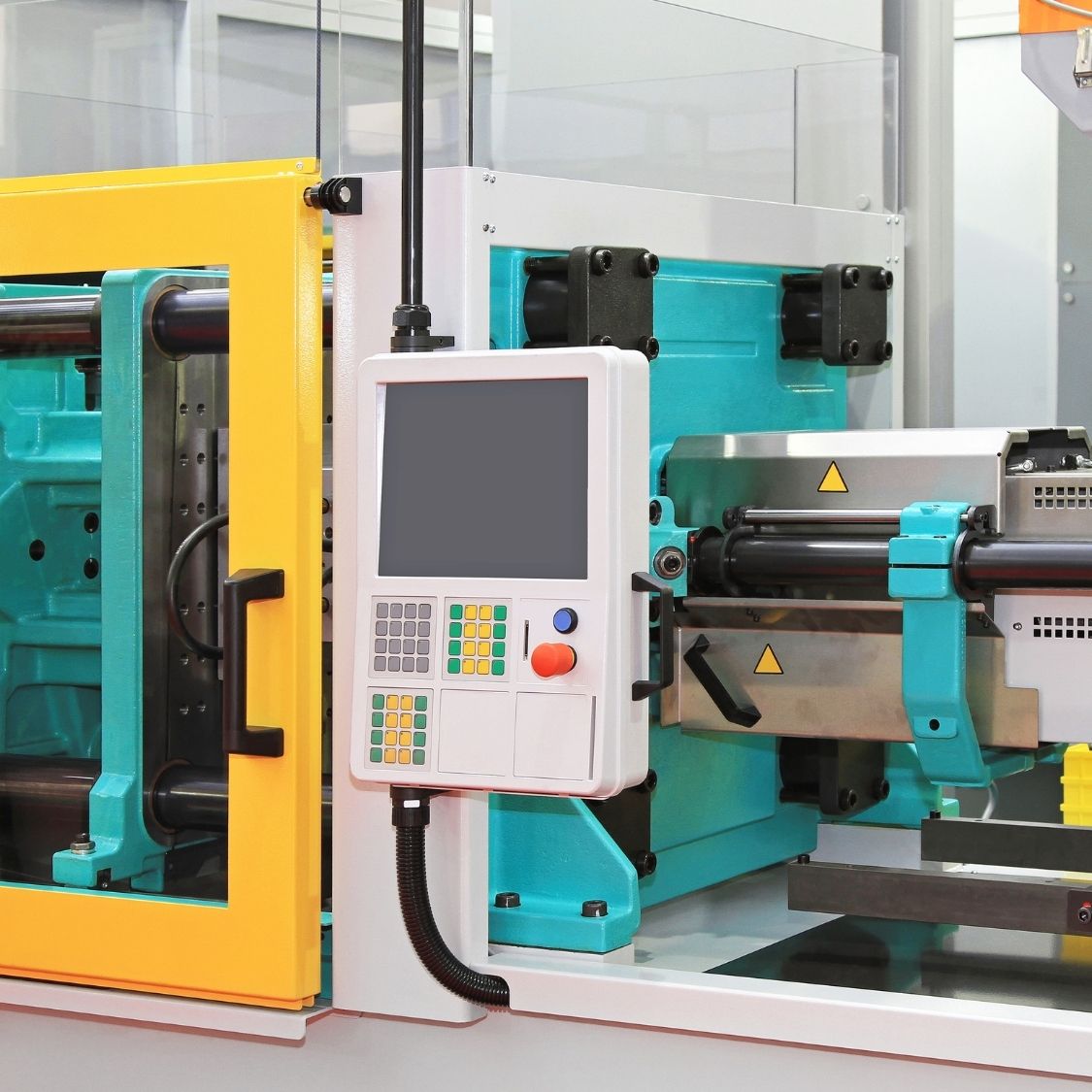
Reaction injection molding is a popular manufacturing process used across several industries. The process is used on automotive parts such as fenders and bumpers to medical equipment. There are also a myriad of items that can be encapsulated with RIM, such as batteries and antennas. As hinted by its popularity, the benefits of reaction injection molding are numerous. But first, what exactly is RIM?
Defining RIM
Reaction injection molding (RIM) is similar to injection molding, except that RIM materials are placed into the mold as low-temperature liquids. Once the liquids are poured into the mold, chemical reactions occur. This reaction creates durable, lightweight, and complex components with relative ease. Designers also have more freedom in designing products made through the RIM process, resulting in more innovative items.
The benefits listed in RIM’s definition are only the tip of the iceberg. Below is a list of other benefits of reaction injection molding:
Cost-Effectiveness
Reaction injection molding is more cost-effective than other manufacturing processes for numerous reasons. For one, RIM is more affordable for lower production volumes than traditional injection molding. In addition, the tooling required by RIM is less expensive than tooling required for injection molding. RIM is more affordable in terms of labor costs, as fewer laborers are required to do the job than there are in the injection molding process.
Design Freedom
RIM gives designers and engineers more design freedom when brainstorming innovative products. For instance, RIM allows for the creation of one product with varying wall thicknesses. This means engineers don’t have to design multiple different parts of different thicknesses. In the same vein, RIM gives manufacturers the ability to consolidate parts, whereas sheet manufacturing does not.
Environmentally Friendly
Another benefit of reaction injection molding is that it is environmentally friendly. The RIM process requires less energy consumption than traditional injection molding, making it a great green option for manufacturers.
More Floor Space
Injection molding equipment tends to take up quite a bit of floor space. RIM equipment, on the other hand, does not. That means facilities with RIM equipment enjoy more precious floor space.
More News From This Category
Tue, 08 Jul 2025 04:16:33 +0000
Welcome to RobinsPost.com's celebration of Amazon Prime Day 2025! From July 8 to July 11, shoppers can enjoy four days of incredible deals across tech, fashion, home goods, and more. We've rounded up the best offers from Amazon and its top competitors to help you save big this summer.
What Is Amazon Prime Day?
Amazon Prime Day was launched on July 15, 2015 to celebrate Amazon's 20th anniversary.
Designed as a mid-summer shopping event, it offered exclusive deals to Prime members across multiple categories.
Why Amazon Created It
- To reward loyal Prime members
- To attract new subscribers and boost Prime memberships
- To test logistics ahead of peak holiday shopping seasons
- To boost sales during a traditionally slow retail month
How Prime Day Has Grown
- Started as a 24-hour sale in 9 countries
- Now spans multiple days globally across 20+ nations
- Includes events like Prime Big Deal Days in October
Prime Day has become a cornerstone of Amazon’s retail calendar, matching the hype of Black Friday, while shaping how competitors respond with their own summer sales events.
Read More ...
Mon, 30 Jun 2025 13:52:28 +0000
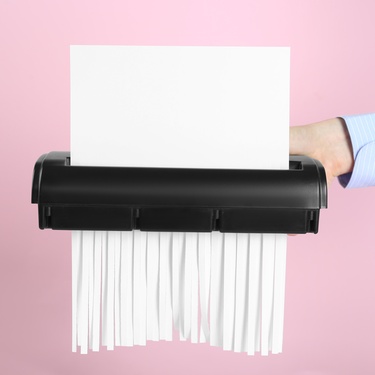
Shredders are a staple in offices and homes for securely disposing of sensitive documents, but they can do much more than rip paper to shreds. Expand your idea of what these powerful tools can handle, and you might find new ways to declutter and organize.
Read More ...
Sun, 29 Jun 2025 15:57:09 +0000
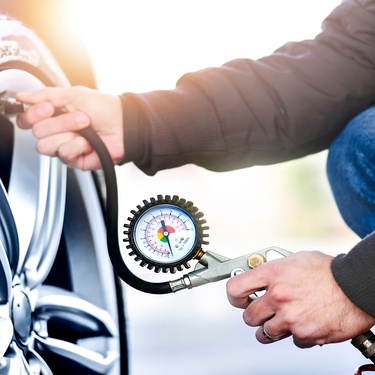
Your vehicle’s tires are its foundation, quite literally connecting you to the road. Ignoring tire pressure readings may seem like a minor oversight, but it can have significant consequences.
Read More ...
Sat, 28 Jun 2025 15:46:10 +0000
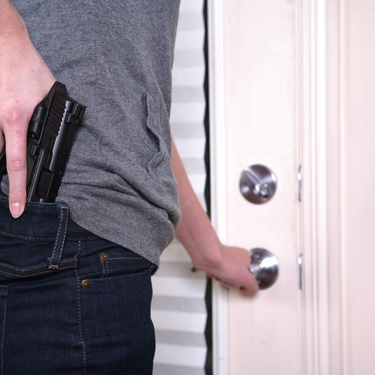
Keeping your home safe is about peace of mind for you and your family. Proactively defending your home wards off potential intruders, safeguards valuables, and protects your loved ones. Defend your home with these impressive strategies that you can implement right now.
Read More ...
Sat, 28 Jun 2025 04:22:40 +0000
Ah, the 4th of July. That magical time when grills sizzle, flags wave, and the night sky erupts in a glittery celebration of freedom. But before you dive into a pool of potato salad and patriotic playlists, let’s take a moment to explore why we celebrate, how we’ve celebrated through the ages, and how to make the most of this all-American holiday—whether you’re hitting the road or chilling at home.
Read More ...